Woodlands’ holistic process is a critical distinction from tree services and woodworkers.
Our interest in the nature and history of the trees, fueled by concern for the environment is the foundation of company.
We start out with a tree that has been targeted for felling- or is already down – and take that wood all the way to the products you see in our shop.
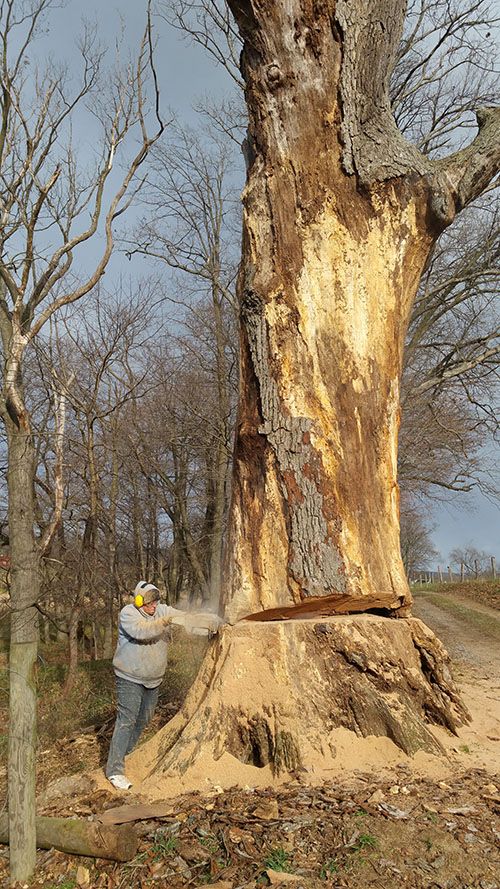
Not a “tree service” that merely removes trees, Woodlands works with homeowners to address their needs and interests. Often we find people have a sentimental attachment to their trees (even if they have caused property damage!). Preserving the sense of respect and value the owners have for the tree is important to us. Some tree services just dispose of the logs once a tree is removed. Keeping track of the origin, Woodlands will “re-claim” that wood into useful and attractive products that will last for decades.
Once the logs are sized to fit on Fiona, the sawmill, (link to Fiona article) the process of milling the logs into board begins. Evaluating each log for its shape & grain patterns, informs how the log is 1st placed on the mill. The first cuts will be to create the flat surface to ensure straight boards. The log is flipped onto the cut side and the milling begins. With each slab, the board is checked to evaluate optimum board strength and/or optimum pattern and color, depending on the planned or most likely use for this wood. Of course, there are tree segments that are not suitable for milling, or because of their unusual shape and marking may be best used for working into objects that require blocks or chunks, like bowl, cups or artwork.
The boards will have a high moisture content – less so if they have been sitting for a while – and need to be dried. Boards must be stacked with wood strips properly – “stickers” – properly placed in between each board to allow air to circulate and even pressure for uniform drying and reduce cracking & slitting. Drying may occur organically or heat and forced air are used for a faster and more controlled drying process.
The dry boards will have tightened, twisted and warped as moisture is lost in the drying process. The surface is rough cut from the mill. To prepare them for building, they need to be straightened, cut to usable sizes and finished. Genie, the 1880’s planer, an example of old being well built heavy-duty and reliable, is the first step. She can handle boards up to 20″ wide and can plane off greater thickness at a time than the sandpaper planer. Again, we need to create a perfectly flat & level surface to start the dimensioning process for the end result to be true. Using the custom planer sled*, the board is balanced underneath to be as close to flat on top, then run through the planer until it is perfectly flat. Then, flipped to the flat side, it is planed again, until the second side is also flat, giving a parallel-sided board. The board will then be run through the sandpaper plane to smooth and more precisely size the board. The next step is to determine the width of the board. Now you can see the details of the grain and patterns in the wood. Uneven edges are trimmed off with the table saw to meet the specifications for the proposed use. * Woodlands has built several pieces of equipment designed to meet the specific requirements of our process and to increase our production capacity and speed. (See Our Equipment)
Since Woodlands uses wood from specific trees in many of our projects, selecting the dimensioned wood for a project requires careful planning. Determining the specific boards and wood is critical. Then, plotting out the needed pieces requires considering size, the appearance, strength and layout. Here, modern technology helps out with software to maximize the number of piece to cut form each board. Measurement must be precise & the woodworkers mantra of “measure twice, cut once” looms large. Depending on the nature, and scope of the project, all the tools in Woodlands “arsenal” are called into service: multiple saws, sanders, routers, clamps, etc. etc.
After all this time and effort, finishing can’t be “slap on some paint and be done with it”. While we finish to meet our customer’s desire, our intention is for the wood to be displayed at it best. Stains and finishes that bring out the colors, patterns and unique characteristics of each hand-built piece add the crowing touches. Again, protecting our environment (so more trees can grow strong) dictates use of non-toxic finishing products. The result is quality wood products that are both utilitarian and beautiful!